Sandwich panels



Specifications
-
Panel sizes 8000 x 2550 x 120
-
Facings made of GRP
-
Core material PUR, PVC, PET and honeycomb
-
Inlays of wood, steel, aluminium or plastic possible
Infos / FAQ (PDF)
Further own products
-
WEMO meter box
-
GRP / FCP repairs
Various versions
Thanks to our modern equipped sandwich panel department, we are able to produce panels in a wide variety of designs, such as:
Cover layers
GRP CFRP Aluminium sheet Steel sheet Wood etc.
Core
PUR PVC EPS PET Rohacell
Messures
to 8200 x 2700 x 250 mm
Applications
Vehicle construction machine industry building etc.
Sandwich panels consist of a core material (foam, honeycomb, etc.) and cover layers glued on both sides. Both the core material and the cover layers are responsible for ensuring mechanical strength. It should be mentioned that the ratio of face sheets to core material must be correct. Bonding a high-strength foam core e.g. with thin thermoplastic sheets (low inherent rigidity) is just as pointless as bonding a foam core with a density (RW) of 15 kg/m3 (low inherent rigidity) with thick chrome steel sheets (high inherent rigidity).
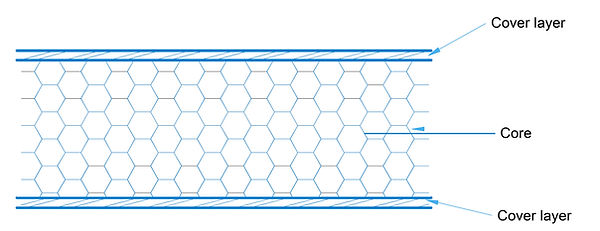
The core material must have such a high inherent stiffness and compressive strength that the distance between the face layers remains constant when the sandwich construction bends. If this is not guaranteed, the bending strength of the sandwich panel collapses abruptly.
The same applies to the adhesive quality. Air pockets in the bond massively reduce the strength values. In addition, these air pockets cause dents to form when the panel heats up (sunlight). For this reason, aXpel composites sandwich panels are bonded under vacuum and the foam cores are pre-grooved so that no air can be trapped. Vacuum bonding guarantees a clean bond, even with different foam core thicknesses.
Mechanical strength
A generally valid formula for calculating the mechanical properties of sandwich panels cannot be established. The calculation principles partly listed in the literature are only valid for defined ratios of total thickness, face thickness, core material and face material in relatively narrow ranges. More meaningful are the empirical values that aXpel composites has gathered in over 20 years of manufacturing sandwich panels for the automotive industry, among others. On the following pages you will find guide values for sandwich panels in various applications with load diagrams of various sandwich panels from practice (no laboratory tests).
Load diagram 1 Sandwich panels
Various foam and cover thicknesses
Core material PVC RW 40
Support width 1000 mm
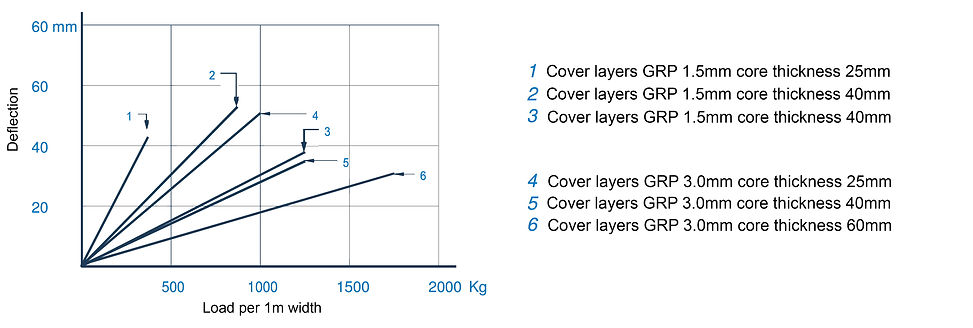
Load diagram 2 sandwich panels
Various core materials and cover thicknesses
Foam thickness 40 mm
Support width 1000 mm

Structure
Theoretically, sandwich panels can be produced with almost all adhesive materials. For road vehicle construction, it has proven itself in recent years:
Cover layers
For large surfaces mainly GRP sheets with
glass content of 20 to 30%, thickness 1 to 3 mm
Aluminium, 0.7 to 2 mm
Steel normal or stainless, thickness 0.7 to 2 mm
For high quality applications Carbon fibre reinforced epoxy sheets
Metals are usually more problematic to bond, and the sheets are not always available in the desired size. Bumps on the plate, even if they overlap, tend to leak water.
Core material
PVC, cross-linked and non-cross-linked, RW 40 to 80 Kg/m3,
PET RW 60 and RW 100 Kg/m3
For static applications also
-
PUR, RW 40 to 60 Kg/m3,
-
EPS, RW 20 to 40 Kg/m3
Honeycomb panels are rarely used because on the one hand the price is much higher than foam and on the other hand the thermal insulation (K value) is worse. For applications where high bending strength is required, the honeycomb core is very suitable.
Other materials can also be used for special designs. A symmetrical structure is advantageous.
Messures
Standard dimensions per panel up to 2 600 mm x 8 100 mm, thickness 120 mm. Larger dimensions are possible.
Inlays
The most cost-effective variant is a panel without inserts. Where necessary, however, almost any type of inlay can be used, e.g. wood, GRP, aluminium, steel, etc. In the case of refrigerated vehicles, attention must be paid to the cold bridges that may be created. Inlays can also be supplied by the customer.
Thermal insulation
The K value (heat transmission value) depends on the foam core used and the thickness, whereby the differences in foam type are relatively small. With a density of 20 to 50 kg/m3, whether EPS, PUR or PVC, the thermal conductivity λ ranges between 0.03 and 0.04 W/mK. In order to achieve good insulation for the entire structure, it is important to choose the wall thicknesses as large as possible and to pay great attention to the sealing of doors.
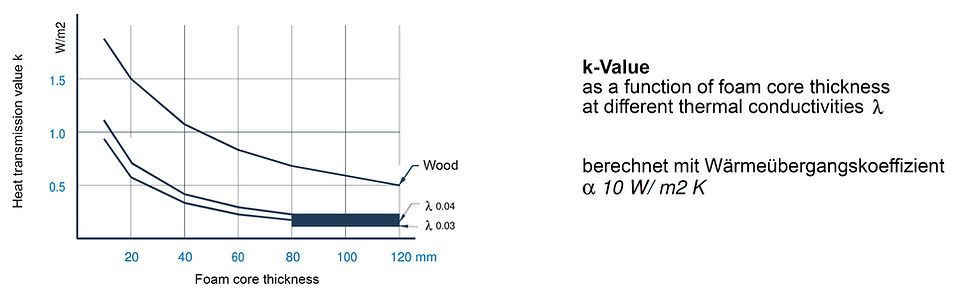
Assembly
The assembly should be chosen in such a way that water cannot penetrate, even if a glued joint is not completely tight. The following points should be observed when gluing:
In the case of glued joints between GRP, aluminium, steel, and also between each other, the adhesive is the weaker link. Therefore, observe the technical data of the adhesive. When bonding foam with foam or with the above-mentioned materials, the foam is usually the weaker link. (Tensile strength of foam approx. 0.2 to 1.5 N/mm2). In the case of corner joints, the glued angle on the inside and outside can also be added to the foam joint. The not inconsiderable dynamic forces that can occur in vehicle construction should not be forgotten.
Fire behaviour
In general, there are no special requirements for the fire behaviour of road transport vehicles. However, it is possible to manufacture elements according to DIN 5510 without any problems.
Shape accuracy, warpage
Large sandwich panels are bonded under vacuum. This guarantees a clean, air-free bond, even for foam panels or inserts with thickness tolerances. Naturally, however, such differences show on one side. The panels should therefore be mounted so that the side with the marks is on the inside.
Storage
When unassembled, sandwich panels should never be exposed to direct sunlight as they may warp due to uneven heat exposure.
Examples, patterns
On the next pages you can see some panels and connection variants. We will be happy to make suggestions for your special needs.
All data without guarantee
aXpel composites sandwich panels
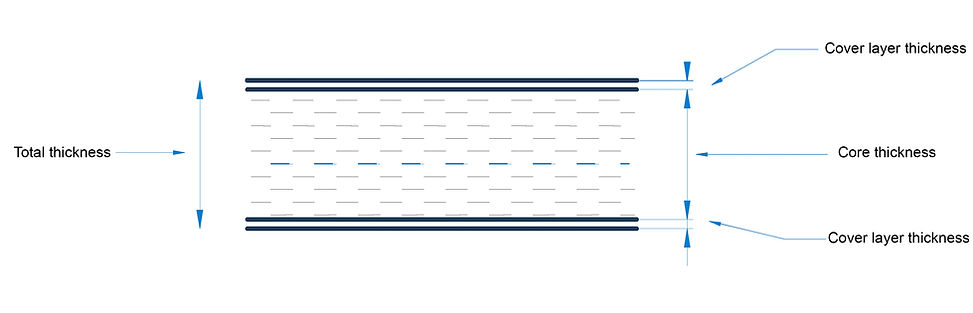
Cover layers
GRP
Aluminium
Steel (also stainless)
Thickness 1.5 to 3 mm
Thickness 1 to 3 mm
Thickness 0.5 to 2 mm
Foam cores
Material
Thickness
PVC
PUR
EPS
10 to 90 mm
RW 40 to RW 90 (RW = Room weight Kg/m3)
RW 40 to RW 80
RW 15 to RW 40
Total thickness
Facings + foam core thickness
Please call us for stock items.
Applications
Vehicle construction
Construction
Electrical industry
for refrigerated vehicles, sales vehicles, special superstructures
e.g. walls, roofs, doors
construction doors, gates, facade elements
Electrical industry Cabinets, walls
Advantages
large-area parts
no panel joints in the top layer
No rust and no oxidation with plastic panels
aXpel composites floor panels with
GRP bottom layer and top laminate
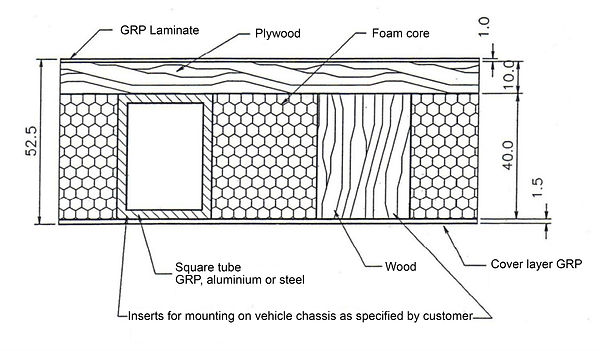
Example:
Total thickness
Underlayer
Top laminate
Foam core
Weight approx.
Size
Applications
Advantages
52.5 mm
GRP 1.5 mm
GRP 1 mm
PVC 40 mm
13 Kg / m2
Floor for refrigerated vehicles
to 2 500 mm x 8 100 mm
Good load capacity, Good thermal insulation
Adhesive bonding of aXpel composites sandwich panels

-
What are the panel sizes?Maximum size of panels that aXpel composites can produce: 2600 x 8100 x 120 mm. Smaller panels possible.
-
What kind of panels are best suited for customer-side processing?Sandwich panels with GRP cover layers are the easiest, also for customer finishing.
-
How thick do the panels for vehicle construction have to be?Depending on the application, between 25 and 40 mm for the side walls and 40 to 60 mm for the roof on cat. A vehicle, for larger vehicles 40 to 60 mm or 60 to 80 mm.
-
How thick do the cover plates have to be?In vehicle construction, GRP facings of 1.5 to 2 mm are common and sufficient.
-
Can other top layers be used besides GRP?It is also possible to use e.g. B. plywood or aluminum sheet. The panel sizes are limited to the sizes of the top layers.
-
What do you take as core material?The most favorable is a foam core made of polyurethane. For higher stresses, a PVC foam can also be used. EPS (exposed polystyrene, Sagex) is also suitable for special purposes. However, care must be taken that this foam core does not come into contact with solvents, otherwise it will dissolve. PET foam is usually used for flame-retardant panels.
-
Are all thicknesses possible?The thicknesses depend on the foam we have in stock.
-
Do the end edges have to be closed?The end faces of sandwich panels must normally always be closed. This can be done by gluing on a U-profile or overlaminating, or as the most expensive variant: gluing in an end profile between the cover layers.
-
What do the mechanical values have to take into account?When designing a component made of sandwich panels, the following points must be taken into account: static load, dynamic load (vehicle construction), weather influences, chemical influences, visual concerns, temperature influences, expansion.
-
What should I pay attention to when gluing?When bonding with other materials, the coefficient of expansion must be taken into account. For expansion coefficient, see "technical data" at www.axpel-composites.ch aXpel composites - GRP sandwich panels can be glued together without any problems. It is essential to observe the bonding instructions of the adhesive supplier.
-
Can the sandwich panels be painted?aXpel composites - GRP sandwich panels can be painted without any problems. It is essential to observe the paint supplier's painting instructions.
-
How do you assemble sandwich panels?Sandwich panels are preferably glued, either at the edge or within the surface. Continuous screw connections are not suitable. If it cannot be avoided, an insert must be glued in, as continuous screwing would compress the foam.
-
Is it possible to install inserts?You can install inlays of various types, be it wood, GRP, aluminum or steel. It is relatively complex and therefore cost-intensive, but in many cases it is the best and therefore also the cheapest solution. In this case, the customer must provide the corresponding drawings, also for a quotation.
-
Is there any other information about aXpel composites - sandwich panels?Yes. You can see a lot more worth knowing in the brochure "aXpel composites sandwich panels in vehicle construction".
-
What are the prices?Please consult our price list.