Sandwich panels

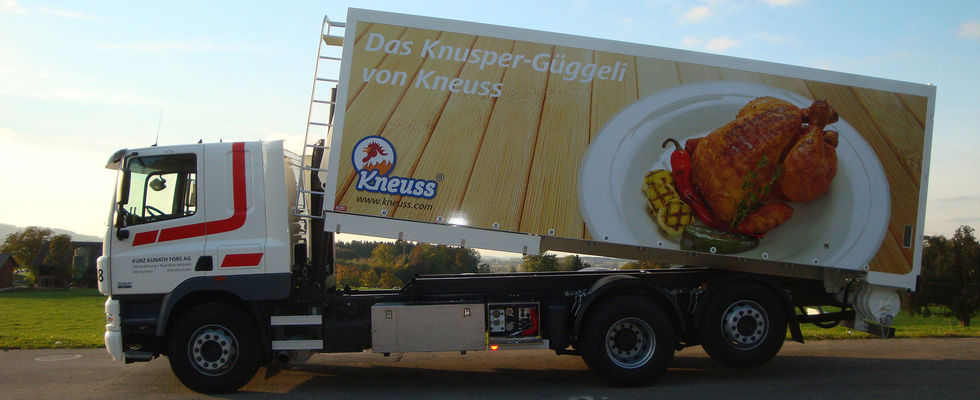

Spezifikationen
-
Plattengrössen 8000 x 2550 x 120
-
Deckschichten aus GFK
-
Kernmaterial PUR, PVC, PET und Waben
-
Einlagen aus Holz, Stahl, Alu oder Kunststoff möglich
Infos / FAQ (PDF)
Weitere eigene Produkte
Verschiedene Ausführungen
Dank unserer modern eingerichteten Sandwichplattenabteilung sind wir in der Lage, Platten in den verschiedensten Ausführungen herzustellen, so zum Beispiel:
Deckschichten
GFK CFK Alu-Blech Stahl-Blech Holz usw.
Kern
PUR PVC EPS PET Rohacell
Masse
bis 8200 x 2700 x 250 mm
Anwendungen
Fahrzeugbau Maschinenindustrie Bau usw.
Der Begriff Sandwich ist zurückzuführen auf den Earl of Sandwich aus dem 18. Jahrhundert. Um seine Finger beim Kartenspielen nicht zu verschmutzen, klemmte er Fleisch oder Käse zwischen zwei Brotscheiben.
Sandwichplatten bestehen aus einem Kernmaterial (Schaum, Waben etc.) sowie beidseitig aufgeklebten Deckschichten. Für die Gewährleistung der mechanischen Festigkeiten sind sowohl das Kernmaterial und die Deckschichten verantwortlich. Hierzu ist zu erwähnen, dass das Verhältnis von Deckschichten zu Kernmaterial stimmen muss. Ein hochfester Schaumkern z.B. mit dünnen Thermoplastplatten (niedrige Eigensteifigkeit) zu verkleben ist ebenso sinnlos wie ein Schaumkern mit einem Raumgewicht (RG) von 15 Kg/m3 (niedrige Eigensteifigkeit) mit dicken Chromstahlplatten (hohe Eigensteifigkeit) zu verbinden.

Das Kernmaterial muss eine so hohe Eigensteifigkeit und Druckfestigkeit aufweisen, dass beim Durchbiegen der Sandwichkonstruktion der Abstand zwischen den Deckschichten konstant bleibt. Ist das nicht gewährleistet, fällt die Biegefestigkeit der Sandwichplatte schlagartig zusammen.
Dasselbe gilt auch für die Klebequalität. Lufteinschlüsse in der Klebung vermindern die Festigkeitswerte massiv. Im weiteren bilden sich durch diese Lufteinschlüsse bei Erwärmung (Sonneneinstrahlung) der Platte Beulen. Deshalb werden aXpel composites -Sandwichplatten unter Vacuum verklebt und die Schaumkerne vorgänig gerillt damit keine Luft eingeschlossen werden kann. Das verkleben unter Vacuum garantiert eine saubere Verklebung, auch bei unterschiedlichen Schaumkerndicken.
Mechanische Festigkeit
Eine allgemeingültige Formel zur Berechnung der mech. Eigenschaften von Sandwichplatten kann man nicht aufstellen. Die zum Teil in der Literatur aufgeführten Berechnungsgrundlagen gelten nur bei definierten Verhältnissen von Gesamtdicke, Deckschichtdicke, Kernmaterial und Deckschichtmaterial in relativ engen Bereichen. Aussagekräftiger sind die Erfahrungswerte die aXpel composites in über 20 Jahren Herstellung von Sandwichplatten für unter anderem die Fahrzeugindustrie gesammelt hat. Auf den nächsten Seiten finden Sie Richtwerte für Sandwichplatten bei verschiedenen Anwendungen mit Belastungsdiagrammen von verschiedenen Sandwichplatten aus der Praxis (keine Laborversuche).
Belastungsdiagramm 1 Sandwichplatten
Verschiedene Schaum - und Deckschichtdicken
Kernmaterial PVC RG 40
Stützweite 1000 mm

Belastungsdiagramm 2 Sandwichplatten
Verschiedene Kernmaterialien und Deckschichtdicken
Schaumdicke 40 mm
Stützweite 1000 mm

Aufbau
Theoretisch können mit fast allen klebbaren Materialien Sandwichplatten hergestellt werden. Für den Strassenfahrzeugbau hat sich in den letzten Jahren bewährt:
Deckschichten
Für grosse Flächen hauptsächlich GFK Platten mit
einem Glasgehalt von 20 bis 30%, Dicke 1 bis 3 mm
Alu, 0.7 bis 2 mm
Stahl normal oder rostfrei, Dicke 0.7 bis 2 mm
Für hochwertige Anwendungen Carbonfaserverstärkte Epoxydharzplatten
Metalle sind meist problematischer zum kleben, auch sind die Bleche nicht immer in der gewünschten Grösse erhältlich. Stösse auf der Platte, auch beim überlappen, neigen gerne zu Wasserundichtheit.
Kernmaterial
PVC, vernetzt und unvernetzt, RG 40 bis 80 Kg/m3,
PET RG 60 und RG 100 Kg/m3
Für statische Anwendungen auch
PUR, RG 40 bis 60 Kg/m3,
EPS, RG 20 bis 40 Kg/m3
Wabenplatten werden selten eingesetzt da einerseits der Preis wesentlich höher ist als Schaum und anderseits die thermische Isolation (K Wert) schlechter ist. Für Anwendungen wo hohe Biegefestigkeiten gefordert sind ist der Wabenkern sehr geeignet.
Für Spezialausführungen können auch andere Materialien eingesetzt werden. Von Vorteil ist ein symetrischer Aufbau.
Masse
Standardmasse pro Platte bis 2 600 mm x 8 100 mm, Dicke 120 mm. Grössere Dimensionen sind möglich.
Einlagen
Die kostengünstigste Variante ist eine Platte ohne Einlagen. Wo nötig können aber fast jegliche Art von Einlagen eingebracht werden, z. B, Holz, GFK, Alu, Stahl etc. Bei Kühlfahrzeugen ist auf die ev. dadurch entstehenden Kältebrücken zu achten. Einlagen können auch Kundenseitig angeliefert werden.
Wärmeisolation
Der K Wert (Wärmeübergangswert) ist vom eingesetzten Schaumkern und der Dicke abhängig, wobei die Unterschiede im Schaumtyp relativ klein sind. Bei Raumgewicht 20 bis 50 Kg/m3, ob EPS, PUR oder PVC, bewegt sich die Wärmeleitzahl λ zwischen 0.03 bis 0.04 W/mK. Um eine gute Isolation für den ganzen Aufbau zu erreichen ist es wichtig die Wandstärken möglichst gross zu wählen und der Abdichtung von Türen ein grosses Augenmerk zu widmen.
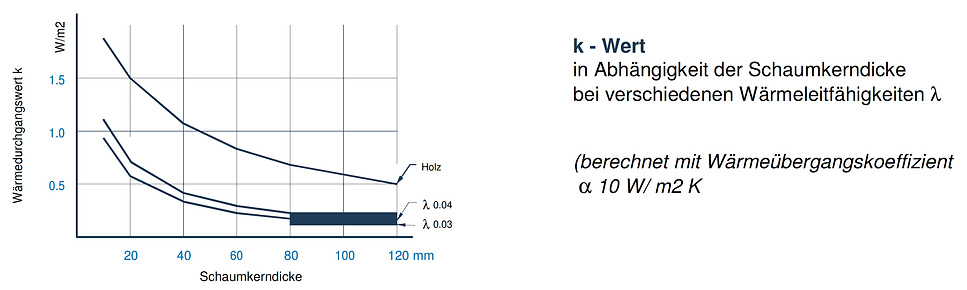
Zusammenbau
Den Zusammenbau soll man so wählen, dass Wasser zwangsläufig möglichst nicht eindringen kann, auch wenn eine Klebfuge nicht ganz dicht ist. Zum kleben ist folgendes zu beachten:
Bei Klebfugen zwischen GFK, Alu, Stahl, auch untereinander, ist der Kleber das schwächere Glied. Deshalb die Technischen Daten des Klebers beachten. Bei verkleben von Schaum mit Schaum oder mit obgenannten Materialien ist meist der Schaum das schwächere Glied. (Zugfestigkeiten von Schaum ca. 0.2 bis 1.5 N/mm2). Bei Eckverbindungen kann zu der Schaumverbindung auch der ev. aufgeklebte Winkel innen und aussen mitgerechnet werden. Nicht vergessen werden dürfen die nicht unerheblichen dynamischen Kräfte die im Fahrzeugbau auftreten können.
Brandverhalten
Im allgemeinen werden für Strassentransportfahrzeuge keine besonderen Anforderung betreffen Brandverhalten gestellt. Doch ist es problemlos möglich, Elemente nach DIN 5510 herzustellen.
Formgenauigkeit, Verzug
Grossflächige Sandwichplatten werden unter Vacuum verklebt. Das garantiert, auch bei Schaumplatten oder Einlagen mit Dickentoleranzen, eine saubere, luftfreie Verklebung. Naturgemäss zeichnen sich aber solche Differenzen auf der einer Seite ab. Die Platten sind deshalb so zu montieren dass die Seite mit den Abzeichnungen auf die Innenseite zu liegen kommt.
Lagerung
In unmontiertem Zustand sollen Sandwichplatten nie der direkten Sonnenbestrahlung ausgesetzt werden da sie sich, infolge der ungleichmässigen Wärmeeinwirkung, verziehen können.
Beispiele, Muster
Auf den nächsten Seiten sehen Sie einige Platten und Verbindungsvarianten. Für Ihre spezielle Bedürfnisse unterbreiten wir Ihnen gerne Vorschläge.
alle Angaben ohne Gewähr
aXpel composites Sandwichplatten
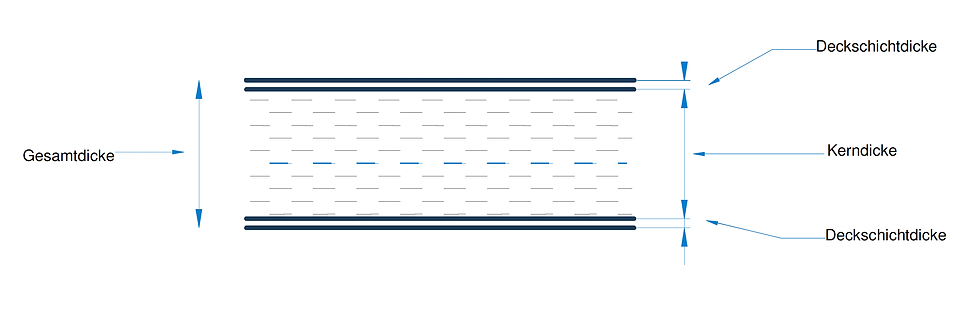
Deckschichten
GFK
Alu
Stahl (auch rostfrei)
Dicke 1.5 bis 3 mm
Dicke 1 bis 3 mm
Dicke 0.5 bis 2 mm
Schaumkerne
Material
Dicke
PVC
PUR
EPS
10 bis 90 mm
RG 40 bis RG 90 (RG = Raumgewicht Kg/m3)
RG 40 bis RG 80
RG 15 bis RG 40
Gesamtdicke
Deckschichten + Schaumkerndicke
Betreffend Lagerware rufen Sie uns bitte an.
Anwendungen
Fahrzeugbau
Bau
Elektroindustrie
für Kühlfahrzeuge, Verkaufswagen, Spezialaufbauten
z.B. Wände, Dächer, Türen
Bau Türen, Tore, Fassadenelemente
Elektroindustrie Schränke, Wände
Vorteile
grossflächige Teile
keine Plattenstösse in der Deckschicht
bei Kunststoffplatten kein Rost und keine Oxydation
aXpel composites Bodenplatten mit
GFK-Unterschicht und Oberlaminat
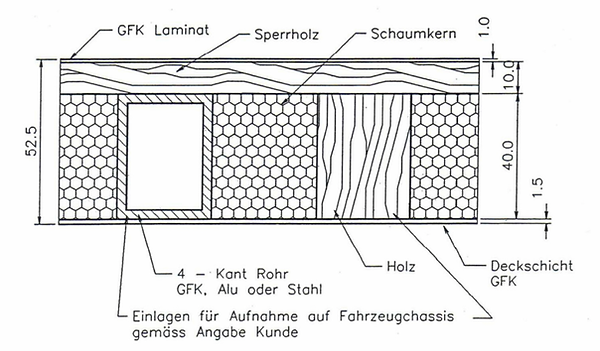
Beispiel:
Gesamtdicke
Unterschicht
Oberlaminat
Schaumkern
Gewicht ca.
Grösse
Anwendungen
Vorteile
52.5 mm
GFK 1.5 mm
GFK 1 mm
PVC 40 mm
13 Kg / m2
bis 2 500 mm x 8 100 mm
Boden für Kühlfahrzeuge
Gute Tragfähigkeit, gute thermische Isolation
Klebeverbindung von aXpel composites Sandwichplatten

-
What are the panel sizes?Maximum size of panels that aXpel composites can produce: 2600 x 8100 x 120 mm. Smaller panels possible.
-
What kind of panels are best suited for customer-side processing?Sandwich panels with GRP cover layers are the easiest, also for customer finishing.
-
How thick do the panels for vehicle construction have to be?Depending on the application, between 25 and 40 mm for the side walls and 40 to 60 mm for the roof on cat. A vehicles, for larger vehicles 40 to 60 mm or 60 to 80 mm.
-
How thick do the cover plates have to be?In vehicle construction, GRP facings of 1.5 to 2 mm are common and sufficient.
-
Kann man auch andere Deckschichten ausser GFK einsetzen?Möglich ist auch der Einsatz von z. B. Sperrholz oder Alublech. Die Plattengrössen beschränken sich auf die Grössen der Deckschichten.
-
What do you take as core material?The most favourable is a foam core made of polyurethane. For higher stresses, a PVC foam can also be used. EPS (exposed polystyrene, Sagex) is also suitable for special purposes. However, care must be taken that this foam core does not come into contact with solvents, otherwise it will dissolve. PET foam is advantageously used for flame-retardant panels.
-
Are all thicknesses possible?The thicknesses depend on the foam we have in stock.
-
Do the end edges have to be closed?The end faces of sandwich panels must normally always be closed. This can be done by gluing on a U-profile or overlaminating, or as the most expensive variant: gluing in an end profile between the cover layers.
-
What do the mechanical values have to take into account?When designing a component made of sandwich panels, the following points must be taken into account: static load, dynamic load (vehicle construction), weather influences, chemical influences, visual concerns, temperature influences, expansion.
-
What should I pay attention to when gluing?When bonding with other materials, the coefficient of expansion must be taken into account. For expansion coefficient, see "technical data" at www.axpel-composites.ch aXpel composites - GRP sandwich panels can be glued together without any problems. It is essential to observe the bonding instructions of the adhesive supplier.
-
Can the sandwich panels be painted?aXpel composites - GRP sandwich panels can be painted without any problems. It is essential to observe the paint supplier's painting instructions.
-
How do you assemble sandwich panels?Sandwich panels are preferably glued, either at the edge or within the surface. Continuous screw connections are not suitable. If it cannot be avoided, an insert must be glued in, as continuous screwing would compress the foam.
-
Is it possible to install inserts?You can install inlays of various types, be it wood, GRP, aluminium or steel. It is relatively complex and therefore cost-intensive, but in many cases it is the best and therefore also the cheapest solution. In this case, the customer must provide the corresponding drawings, also for a quotation.
-
Is there any other information about aXpel composites - sandwich panels?Yes. You can see a lot more worth knowing in the brochure "aXpel composites sandwich panels in vehicle construction".
-
What are the prices?Please consult our price list.